Aranet is a brand of SAF Tehnika JSC (SAF1R.RG), one of the leading microwave data transmission equipment manufacturers in the world with a presence in over 130 countries. Our 20+ years of experience in information technology has enabled us to build a truly unique and innovative Aranet radio that powers our entire Aranet ecosystem.


Aranet IoT ecosystem is a truly unique player in the wireless sensor market. We design, manufacture and develop a complete solution - sensors, a 3-in-1 base station (gateway, data storage & web server) and a cloud.
SMART Tools for Smart Businesses. No matter what industry your are in, or what you are eager to measure - we got you covered.
Smarter Indoors
​
Poor air quality can negatively affect your well-being and health. Aranet ecosystem offers a high-quality monitoring solution to stop guessing and measure what's important.
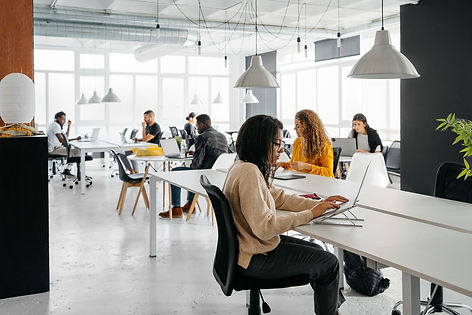
Ventspils City Council installed 475 Aranet4 CO2 meters across all schools and kindergartens in their city. The impact was immediate as real-time information enabled staff to act without delay.
2. Smarter Horticulture
​
Our Aranet ecosystem is not just a combination of hardware and software. It’s a way to communicate with your greenhouse and stop the game of guessing
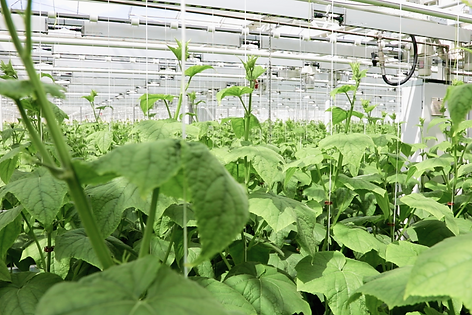
Getlini EKO is one of the most advanced greenhouses in the world that uses LED lighting to grow cucumbers. By installing Aranet sensors, their yield increased by a staggering 20%
3. Smarter Livestock
​
A healthy environment is key for your livestock and business to thrive. Aranet ecosystem offers a high-quality monitoring solution to stop guessing and measure what’s important.

Balticovo, the largest egg manufacturer in Northern Europe, chose the Aranet monitoring solution to ensure their chickens thrive in a healthy environment. The better you treat your chickens, the healthier and more productive they will be, significantly improving the parameters which are important in their business.
4. Smarter Retail
​
Avoid food spoilage and save resources with Aranet wireless monitoring solution. It offers centralized and automated temperature tracking across all your stores
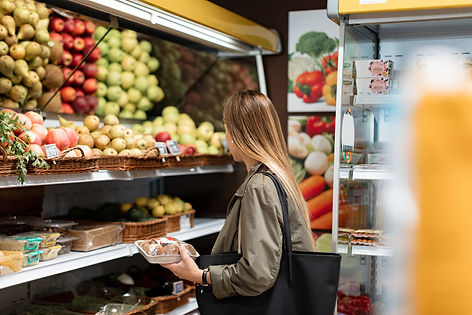
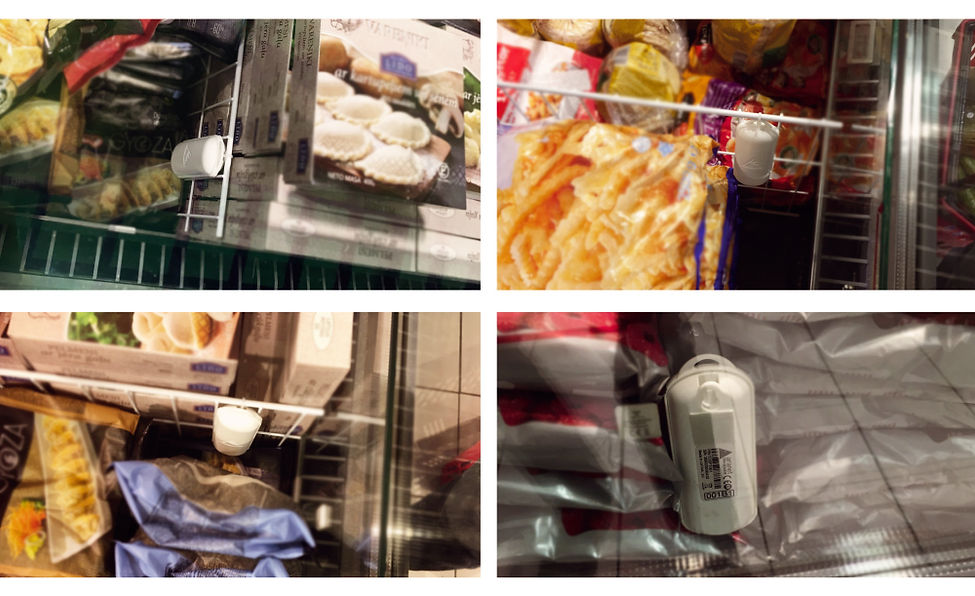
Saved time & resources – Centralized data gathering freed up employees' time by automating manual documentation processes and avoiding human error. The company could now manage its temperature quality control with fewer employees overseeing the operation.
​
Avoided food spoilage – temperature data was collected 24/7 with no interruptions. That allowed the company to see the full scope of the temperature data and analyze its operations over time. If the desired temperature thresholds were crossed, the system would automatically send E-mail alerts to the responsible personnel.
Compliance with regulation – Keeping digital records about the conditions in which produce is stored is essential to comply with food safety regulations. Centralized data collection allowed the company to stop using clumsy paper reporting.